Research and development, scale-up and technology transfer
Early stages of development:
- design and creation of expression vectors by genetic engineering methods,
- transfection of expression cells,
- screening, clonal selection and stability studies of therapeutic protein producing cell lines,
- preparation of therapeutic protein producing cell banks and analytical cell banks,
- development of laboratory scale processes for the production of therapeutic proteins in the field of cell culture (upstream) and purification of products using filtration and chromatographic methods (downstream),
- scaling up of therapeutic protein manufacturing processes,
- QTPP (Quality Target Product Profile) determination for biosimilar products,
- development, qualification and validation of analytical methods for determining the efficiency of manufacturing processes, purity, quality and activity of medicinal products, and in the case of biosimilars – verifying the degree of biosimilarity.
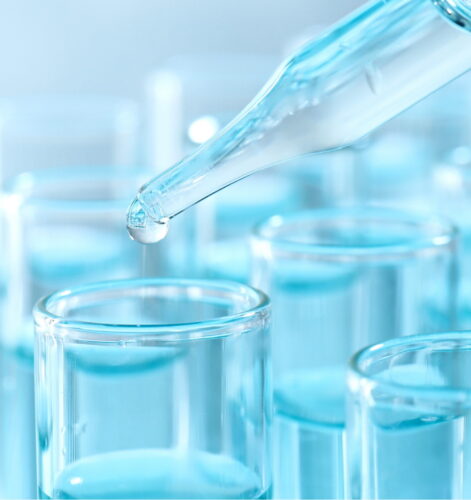
Scale-up processes
For manufacturing from 500L to 5000L scale , we support the Manufacturing and Quality Control Departments with our research in the following areas:
- determination of acceptance criteria (PAR – Proven Acceptable Range, NOR – Normal Operating Range) for individual process parameters, determination of critical product quality attributes (CQA), critical process parameters (CPP), key process parameters (KPP),
- process characterization and determination of the process space for individual stages of drug product manufacturing (SDM, OFAT, QbD),
- testing the purity, quality and stability of active substances and finished products.
We conduct our research in accordance with the principles of Good Manufacturing Practice (GMP), Good Laboratory Practice (GLP), and Good Documentation Practice (GDP). We use unique and modern technologies to ensure that our testing processes are of high efficiency and quality. All of our equipment meets the requirements of EMA and FDA regulatory agencies, including: FDA 21 CFR Part 11 standards. We use high quality reagents and materials from proven, world-class suppliers.
Cell cultures
As part of the development of therapeutic protein expression processes, we conduct work using qualified small-scale models.
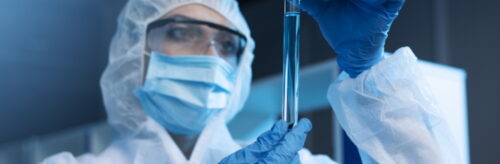
We monitor cell culture parameters using high throughput systems, which guarantee the possibility of obtaining large amounts of data in a short time. Additionally, measurements are very precise and accurate and can be performed continuously. The results are read out using laser technology.
Clonal evaluation and selection
In the process of derivation of cell lines producing therapeutic proteins, it is extremely important that the line is monoclonal, stable, highly productive and that the resulting product has a quality profile that is consistent with expectations.
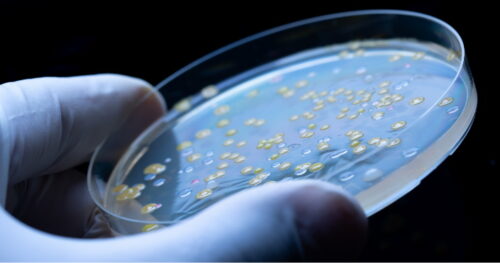
Experience and knowledge are extremely important in these processes, but here too we make use of the latest technological developments. We support the work of our scientists with high-throughput systems in the following areas: clonal selection of cells from heterogeneous populations. Thanks to the combination of knowledge and technology, we are able to select clones with the highest productivity, which is an important attribute for industrial applications. Cell growth after selection is monitored and documented automatically.
Orbitally shaken bioreactors
We have unique bioreactors in our cell culture development laboratories that allow for culture with orbital shake technology, in which we conduct both scale-up and characterization of cell cultures.
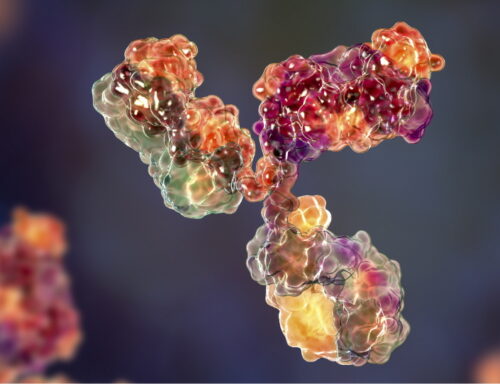
Orbitally shaken bioreactors are characterized by the absence of mechanical stirrers and systems of aeration directly into the liquid – mixing and oxygenation of the culture is based solely on orbital motion. Bioreactors with a working volume of 12 L allow us to pre-select process parameters that are not possible to determine on a smaller scale, such as 50 mL. They are a faithful replica of production bioreactors with working volume
of 2500 L, which are located in the Manufacturing Department.
With these bioreactors we can reliably verify the impact of changes in the manufacturing process on the resulting product. The cultures in our bioreactors are conducted using only single-use materials, without contact of the culture fluid with the bioreactor, which ensures high purity of the product and minimizes the risk of contamination.
Composition of the culture media
During the development of culture conditions for antibody-producing cells, testing the levels of nutrients in the culture media and metabolic secreted by the cells during culture plays an important role.
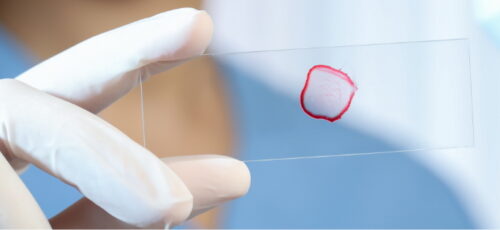
For this purpose, we use fully automated, high-throughput equipment that allows us to perform several hundred tests within a few hours. The analysis of the content of culture fluid components is performed on the basis of enzymatic reactions and colorimetric measurements. Thanks to that, we can choose appropriate conditions of cell supplementation, to increase the efficiency of the culture and improve the quality of the obtained product. We also monitor the content of metabolites that may have a negative impact on cell growth and viability.
Purification of proteins
In the development of purification processes, we use preparative systems that have their counterparts on industrial scales. We use them to develop methods and processes, as well as to select optimal chromatographic compositions and optimize processes.
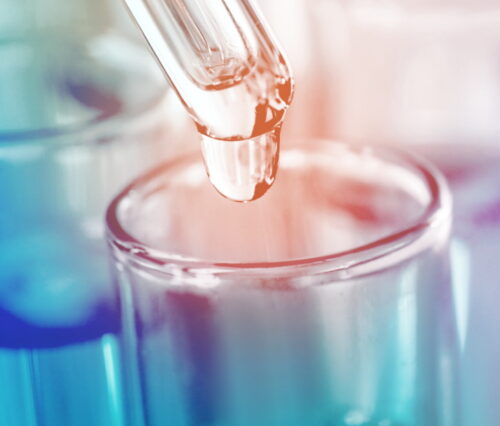
For design of experiments (DoE) as well as their control we use advanced, specialized software that is tailored to our process equipment. Our attention to experimental work results in high performance of the processes we develop.
Thanks to the appropriate design and software, these devices ensure control over the process conditions, as well as their proper monitoring and data archiving. Additionally, we are able to simulate the future course of processes on a laboratory scale down models to the smallest detail. This reduces the time of process implementation as well as the cost of transfer.
Biosimilarity studies
In order to prove that the obtained product has the appropriate quality characteristics (confirming its biosimilarity to the reference drug), a number of physicochemical and biological analyses are performed. They allow for comprehensive structural and functional characterization of protein products.
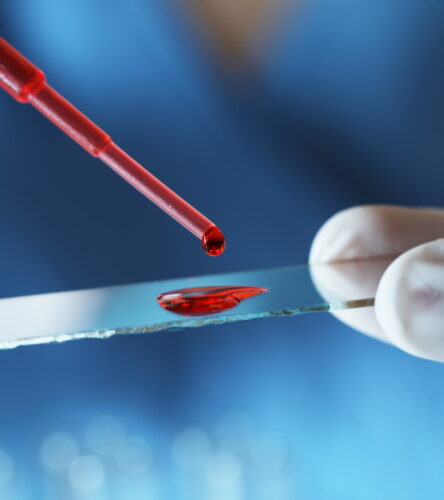
Our laboratories are equipped with cutting edge analytical systems. Through their use, we are able to develop, qualify and validate high-quality analytical methods that meet the requirements of regulatory agencies.
We evaluate critical protein quality attributes (e.g., glycosylation profile and aggregate levels) using modern high-performance and ultra-high performance liquid chromatography (HPLC, UHPLC) systems. Our UHPLC systems Thermo Scientific™ Vanquish™ and Thermo Scientific™ UltiMate™ 3000 are fully integrated and biocompatible, equipped with three types of detectors: a diode array UV-VIS detector, a fluorescence detector and a corona discharge detector. The Thermo Scientific™ UltiMate™ 3000 UHPLC system is also coupled to a mass spectrometer.
We use the mass spectrometer in a very wide range of applications, based on bottom-up, middle-down and top-down strategies. It is used to determine the amino acid sequence of proteins, measure the mass of the whole antibody and its subunits, determine disulfide bridges and analyze post-translational modifications. Such comprehensive product characterization is possible thanks to the laboratory being equipped with a modern, high-resolution Thermo Scientific™ Q Exactive™Plus Biopharma mass spectrometer. This is a tandem mass spectrometer (equipped with a quadrupole analyzer and an Orpitrap™ analyzer) with a resolution capacity of up to 280,000.
For antibody purity determination, we use a Beckman Coulter™ CESI 8000 Plus capillary electrophoresis system with modular, interchangeable UV-VIS and LIF detectors. The system also allows connection to a mass spectrometer.
We use the Biacore™ T200 System to measure interactions between molecules, determine affinity and both association and dissociation rate constants. The system is based on the Surface Plasmon Resonance (SPR) phenomenon. It is a state-of-the-art device which enables real-time investigation of biomolecule interactions without the need for sample labeling.
Manufacturing potential
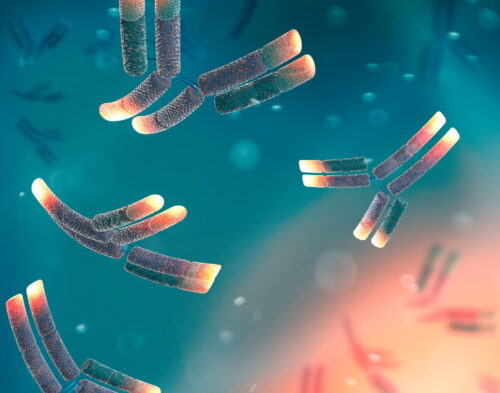
Mabion is the first company in Poland which obtained GMP certification for the production of biotherapeutics in mammalian expression systems. This means that we are the most experienced team in this field in Poland and in Central and Eastern Europe.
Mabion has a sterile formulation plant for biotech products that is GMP-certified. Here we combine scientific knowledge with advanced technology. Our primary goal is to produce biological products through the processes of obtaining recombinant proteins in various expression systems and purification of proteins to the production of sterile finished products.
We use primarily single-use technology. The main advantage of using such systems is the isolation of the product from the production environment, which provides safety and flexibility of production. Additionally, we eliminate the need for cleaning process validation and reduce the time needed to prepare the line for production of subsequent batches of products.
Cell culture stage
We can work with any mammalian, insect and bacterial expression system. We generate and store cell banks in GMP standard. We independently prepare the necessary media and supplements for culture. We are able to perform cell harvesting by centrifugation and various depth filtration methods.
Purification stage
We have a wide range of options for purification of protein products. We conduct affinity and ion exchange chromatographies in both binding and non-binding modes. We are experts in viral filtration, sterilization, and ultra/diafiltration. We prepare thousands of liters of buffers and solutions daily.
Bottling and finished product preparation
We can offer fill and finish in vial format in sterile conditions as well as secondary packaging services. We have our own warehouse and truck fleet, which makes us independent in terms of supply and distribution.
Technologies and equipment
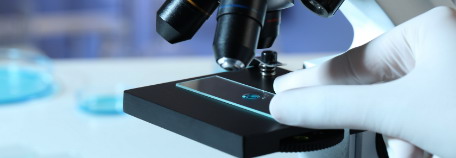
We have modern process equipment at our disposal. We are the first, and so far the only, plant in the world using the 2500L orbital shaker technology.
Our cell culture line consists of incubators, 250L bioreactors and 2500L bioreactors. All of them work with orbital shake technology and allow culture in CO2 atmosphere. We have tools that allow us to thoroughly analyze culture parameters both in terms of their physiological characteristics as well as gas and metabolite content in situ.
We conduct harvest using both centrifugation and depth filtration with the use of various filter types (membrane, glass-fiber, hollow-fiber and others).
We have many years of experience in working with chromatographic systems, both multi-use (ÄKTA Process) and single-use (ÄKTA Ready).
We work with the largest chromatographic columns in Poland and many types of chromatographic compounds. We can easily adapt to the specifics of a given process thanks to the possibility of purifying from a dozen to several thousand liters of product in one batch.
Nanofiltration, ultradiafiltration and formulation processes are carried out within dedicated systems, which ensure constant control of process parameters.
We have unique solutions for buffer and process media transfer. We shorten material transfer paths, so we use less material, media and time. Our processes are time and cost efficient as well as environmentally friendly.